What is Precision Grinding?
Precision grinding is a precision manufacturing process widely used in various fields. Precision grinding provides an effective method to complete the manufacturing and finishing of metal parts with very tight and tight tolerances. It is typically used as the one of final machining processes on a part.
Precision grinding uses grinding wheels as cutting tools. Grinding wheels are consumable grinding wheels for various grinding and abrasive machining operations. Precision grinding uses a rotating grinding wheel to remove material, resulting in a flat surface, which can produce very good finish and very precise dimensions.
Some precision machining factory can perform precision grinding on site, or they can choose to outsource it to companies specializing in this service. Many cities in manufacturing regions and factories have facilities to provide this service. Many of these companies also manufacture and use the specifications provided by customers to produce precision machined parts on order, such as SANS machining.
Since Precision Grinding is an expensive operation, it is used only on materials requiring a better finishing.
Types Of Precision Grinding
The technician will also select the appropriate tool to make the surface of the workpiece to be polished have the correct shape, size and texture.
Depending on the size, shape, features and required productivity, the technician will select the appropriate grinding operation.
- Surface Grinding
- Cylindrical Grinding
- Centerless Grinding
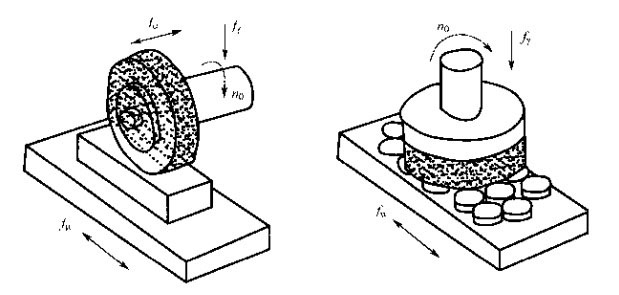
Surface Grinding:
Surface grinding is one of the finishing methods of planes, which can get better machining accuracy and surface quality. Surface grinding is usually carried out on a surface grinding machine. The circumferential surface of the grinding wheel can be used for grinding, or the end surface of the grinding wheel can be used for grinding.
When grinding the circumferential surface of the grinding wheel, the contact area between the grinding wheel and the workpiece is small, the calorific value is small, the cooling and chip removal conditions are good, higher processing accuracy and smaller surface roughness value can be obtained, but the production efficiency is lower . When grinding with the end of the grinding wheel, the contact area between the grinding wheel and the workpiece is large, the heat is large, the cooling and chip removal conditions are poor, the machining accuracy and surface roughness are poor, but the production efficiency is high. In order to improve the grinding efficiency, multiple pieces of grinding are often used.
Cylindrical Grinding:
Cylindrical Grinding, also known as central grinding, used to grind the cylindrical surface and shoulder of the workpiece on the outer or inner diameter, also know as ID & OD grinding. Cylindrical grinding can provide a smooth surface finish on round objects.
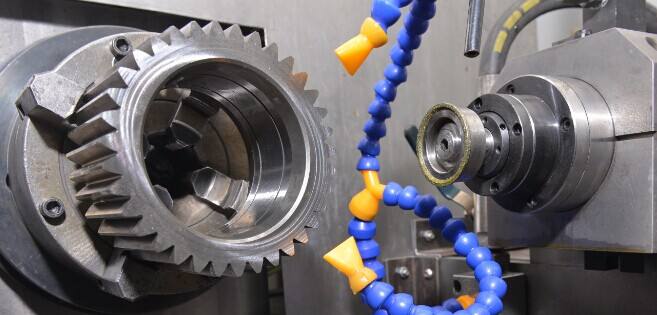
The workpiece is mounted in the center and rotated by a device called a drive claw or center drive. The grinding wheel and the workpiece are rotated at different speeds by separate motors. The table can be adjusted to produce taper.
Cylindrical grinders have a grinding wheel (grinding wheel), two fixed workpiece centers and a chuck, grinding claw or other mechanism for driving the workpiece. Most cylindrical grinders include a turntable to allow the formation of tapered parts. The grinding wheel and the workpiece move parallel to each other in the radial and longitudinal directions to shave.
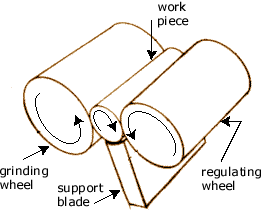
Centerless Grinding
Centerless grinding is usually used to machine long, thin and small workpieces that are not between the spindle and the tailings.
In this grinding operation, the workpiece is fixed between two rotating grinding wheels, the grinding wheel has a high linear velocity, the grinding action is performed on the surface of the workpiece, and the guide wheel drives the cylindrical workpiece to rotate on the horn. The blade supports the workpiece during the machining process.
The extremely precise setting of the machine and the carefully selected grinding tools require extensive knowledge and experience, which is why it is widely used in the automotive, bearing industry, electric motors, toll collection, and textile industries. and many more
In a typical precision grinding process, the grinding wheel grinds the surface to the exact specifications of the project, while always maintaining the highest accuracy. However, in addition to this shaping and shaving, this grinding process also produced a smooth surface with no bumps, bumps or patterns.
Which Parts Need Precision Grinding?
Precision grinding is used for materials with small surfaces. These materials require a high degree of flatness, a high degree of parallelism, or an excellent surface finish. However, there are many larger parts that also require precision grinding, including aerospace instruments, medical equipment, tools with blades, and parts commonly used in many different scientific instruments. These devices are very sensitive, and the allowable error is very small, therefore, every grinding needs absolute perfection. With many years of experience and professional skills, SANS can grind any of these ingredients, and can grind according to your requirements.
Importance of Precision Grinding in Products
This type of grinding provides precise accuracy. Metal manufacturers can use this process to replicate the most specific and subtle measurement results, even to the smallest score.
Precision grinding can be used for products of various sizes because the process has the ability to adapt to exact individual specifications. For industries that have little margin of error (such as parts used in medical equipment, scientific instruments, and aerospace agencies), this accuracy is very important.
Modern electrical equipment is becoming smaller and smaller, which means that the internal metal parts are also being reduced in size, so precision grinding is required for manufacturing. This is a more cost-effective production method than other alternative methods and technologies.
In addition to cost-effectiveness and accuracy, there are many other benefits of using precision grinding. Increased productivity and easy monitoring mean that quality control can be maintained throughout the effective production process. Not only that, it also provides very fine surface finish and high-quality final products.
SANS Precision Grinding
Our grinding systems that can achieve surface finishes to 0.2~0.025 Ra with tolerances as tight as 0.002mm. Detailed tolerance and surface finishes can vary due to material type of both the part and the grinding wheel.
Min ID Grinding diameter : 6.0mm
Max OD Grinding diameter :260mm
Max Surface Grinding Size: 1000mm
If you are looking for a special alloy that needs to fit exact specifications, contact us today to discuss your requirements. Contact Now