In manufacturing, CNC machining has long been used in manufacturing and production. With the advent of technology and computer-aided design software, designing products may become easier, but this makes the design more complex than before. In the design phase itself, you need to set standards for product accuracy, precision and tolerances.
There are too many technical terms related to the specifications and functions of CNC machining. Do you know the meaning of each term? When purchasing CNC machining services from a service provider, you must have heard or read some terms, such as precision, tolerance, accuracy, etc. What do these terms mean? Do you want to know the importance of these technical terms in CNC machining? If so, please read the following article as it will give you a clear understanding of these three terms (precision, accuracy and tolerance).
Machining Precision
What is Precision?
Precision refers to the closeness between measurements, which means that if the measurements are all close to each other, they are precise. Precision means consistent repeatability when producing multiple parts with CNC machine tools. It reflects whether the measured value is repeated and consistent. The higher the precision, the closer the result.
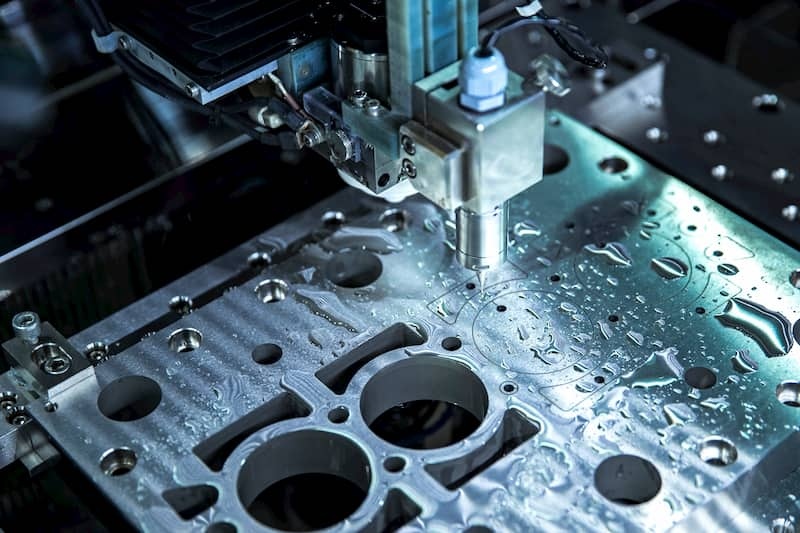
This is one of the most important terms used in CNC machining. Likewise, the term defines the reliability of machine tools. Basically, precision is a metric that defines the ability of the measurement system to return the same metric again and again.
In a factory, the precision of a machine or process refers to the ability to repeat operations in the same way every time without introducing or random errors. Precise machining or precise craftsmanship proves the control of the process without deviation. This is often confused with accuracy and indeed the two terms are casually used interchangeably. However precision refers more to repeatability. (More about precision Machining at The Importance Of High Precision Machining)
Machining Accuracy
What is Accuracy?
Although accuracy and precision seem to be synonymous, they have different meanings during machining processing. Therefore, it is important to know what we mean in different terms.
Accuracy is defined as how close the measured value is to a specific value or true result. If all the measured values are close to the true value, they are accurate. It can reflect the impact of system errors. If the system error is small, the accuracy is high.
In metal machining processing, accuracy refers to the degree to which the machine can match the measured values specified in the design. If the machine can cut the exact position specified in the design, it has high accuracy.
A precise machine that will perform operations (cut, drill, bore, etc.) as the operator/programmer intended. For example, if a machine is programmed to cut a workpiece to 60mm length, it will be cut to 60mm. Accuracy means that it is close to 60mm accurately. The closer to the standard, the higher the accuracy.
Factors Affect CNC Machined Accuracy
Reverse Deviation
When machining a workpiece in a CNC machining workshop, the axis of the shaft causes a reverse dead zone or backlash during the transmission process, causing errors, and its performance is reverse bias. If the CNC machine tool adopts a semi-closed loop servo system, the existence of the reverse offset will affect the positioning accuracy of the machine tool and repeat positioning accuracy, affecting the accuracy of the workpiece.
Gap Error
This is the clearance error caused during the operation of the machine tool drive chain. When the motor is running, the machine tool does not produce movement, which will cause vibration or large errors of the CNC machine tool.
Part Position Error
The position error of the part is the deviation between the actual surface and the shaft position relative to the ideal position, which is mainly based on the head position error caused by the transmission gap of the machine tool and the elastic deformation of the part and the service friction.
In an open-loop system, the position error has a great influence on a machining accuracy, but in a closed-loop servo system, it mainly depends on the accuracy of the displacement detection device and the system amplification factor, so the general effect is not obvious.
Geometric Error Of Machine Tool
In the CNC machining process, tools and fixtures are affected by external forces, and thermal cutting will reduce the volume accuracy of the machine tool, thereby affecting the deformation of the processed parts.
Of course, the causes of machine tool geometric errors are internal and external. The internal reason is the factor of the machine tool itself. For example, the levelness of the table surface and the geometric accuracy of machine tools and fixtures.
The external cause is the external environment and the heat generated during the machining process, which leads to deformation of the machine tool. Changes in temperature will affect the static and dynamic accuracy of the machine. In the machining process of CNC machining factories, the heating of the motor and the friction of the workpiece will cause temperature changes, which will lead to the loss of adjustment accuracy and affect the size and accuracy of the workpiece.
Positioning Error Of Machine Tool
The positioning accuracy of the machine tool will greatly affect the accuracy of the parts. Therefore, the positioning error is an important cause of CNC machining errors, and the feed system of the machine tool is the main link that affects the positioning accuracy. The feed system of a CNC machine tool is usually composed of a mechanical transmission system and an electrical control system, and its positioning accuracy is related to the mechanical transmission system of the structural design.
In the open-loop system, due to more influencing factors and more complicated situations, positioning monitoring will not be possible, which greatly affects the machining accuracy of CNC machine tools. However, in a closed-loop system, CNC machine tools can usually avoid the positional deviation of the main components in the system through positioning detection devices.
The Importance of Accuracy
CNC machined parts are used in many industries. The success of automotive, aerospace, medical, industrial and many other industries depends on accurate products.
Accuracy can also ensure the safety of the public. For example, automobiles and airplanes are composed of various CNC machined parts. If one of these components does not meet company and industry standards, it may have a chain reaction, putting drivers and passengers at risk.
Machining Tolerance
What is Tolerance?
Tolerance can be defined as the allowable or predictable deviation of the measurement system from known or standard values. The tolerance of any system is usually expressed as “+/-“.
For example, the tolerance of CNC machining tools is required to be +/- 0.01 mm. This means that the machining tool will have a deviation of 0.01 mm in each cut. The deviation can be 0.01 mm larger than the standard value or 0.01 mm smaller than the standard value.
Although it is a good idea to reduce the tolerance, sometimes it may not be necessary to reduce the tolerance, and it will not benefit the finished product. But tight tolerances will increase costs and make the manufacturer’s production time longer. Therefore, the acceptable value of the tolerance actually depends on the field of application.
Although the tolerance is defined by the customer, the machine usually specifies its standard tolerance and the smallest possible tolerance.
Factors Affect Machining Tolerance
Materials: Materials behave differently under pressure, and some materials are easier to process than others. These material properties must be considered when determining tolerances.
Machining type: The processing method used will significantly affect the possible tolerances of the final part, because some processes are more precise than others.
Plating and finishing: When determining the size and tolerance of parts, any plating or finishing process should be considered. Although electroplating and finishing will add a small amount of material to the surface of the part, these small amounts will still change the size of the final product, so it should be considered before production.
Cost: Tolerances should be precise, but never exceed the necessary tolerances, because getting tighter tolerances is more costly. (How To Reduce Machining Cost)
The Importance of Tolerance
Today’s manufacturers require strict tolerances to ensure that their products or systems are easy to assemble and perform the required functions with minimal adjustments. From the material of the part to the machining process used, various factors can cause differences. Therefore, engineers assign machining tolerances to parts during the design process, and tolerance is ultimately one of the most important factors in the process from the drawing board to the finished product.
Today’s manufacturers require strict tolerances to ensure that their products or systems are easy to assemble and perform the required functions with minimal adjustments. Correct design specifications can reduce production time and reduce customer costs.
Relationship Between Precision, Accuracy and Tolerance
High precision not means high accuracy, and even if the measurement is accurate. Maximum accuracy and tight tolerance are not necessary for every part, because they means more cost and time investment. Modern CNC machine and cutting tools are accurate enough for most projects.
It’s very intuitive to see the relationship through the following image.
We hope you got an understanding of the terms – accuracy, precision, and tolerance used in CNC machining. This understanding of terms will make you more confident while having a word with any machining service.
Learn more about SANS Machining, our products and our services or get a custom project quote by contacting us today!
It’s helpful that you mentioned that machine tolerance is dependent on the materials I’m working with. I’m considering to hire a plastic CNC machining service soon in order to help in producing a case for my guitar. Using translucent plastic might give it a nice retro look.