With the advancement of science and technology, Wire electrical discharge machining(EDM) technology has developed into an important machining technology in the machining industry, with high machining accuracy and relatively few restricted conditions. The precision of the parts processed by wire EDM is beyond the reach of general machining technology. And the processing range is also relatively wide, basically any metal conductive material can be processed, and it is not limited by the hardness of the material.
By using the electric discharge between the wire EDM and a conductive material such as stainless steel, the desired shape can be obtained. Wire EDM is considered to be one of the most cost-effective methods for machining hard and conductive materials.
Wire EDM does not produce the objective force of other processes during processing. The driving force required by the spindle of all machine tools is relatively small. In this case, only a relatively small motor is required to operate normally, which is correspondingly Improve the processing accuracy of the product.
Wire EDM is becoming more and more popular because of its advantages:
Advantages Of Wire EDM
1. Improve production efficiency
Wire EDM electrodes use 0.03-0.35mm metal wires. With the help of experienced and efficient processing engineers, Wire EDM projects can be set up and completed in a shorter delivery time, so that you can get them faster Key parts. Wire EDM can produce high tolerance parts without burrs or deformation; wire EDM can process production parts in one step, saving you valuable time and money, and greatly improving production efficiency.
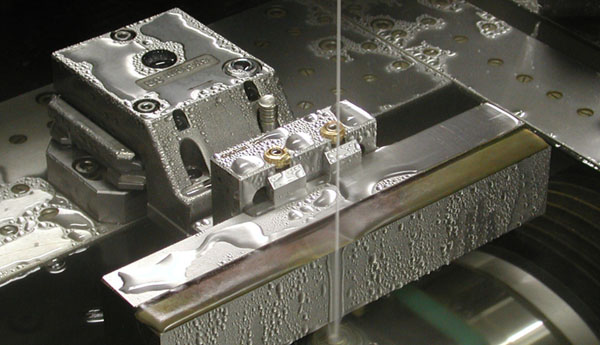
2. No Impact Cutting
The processing of hard materials usually requires intensive processing, which requires a lot of force and impact to form the desired shape during processing. This has some disadvantages, because impacts can create stresses that deform the material during cutting and rapid wear of the tool. This makes traditional machining on precision parts challenging. Wire EDM can process hard and fragile materials, as long as they are conductive, they will not produce impact and stress. Even cutting extremely thin materials will not bend or warp.
3. Wide Processing Range
Wire-cut EDM can also cut the hardness of conductive metals relatively easily, from copper to the hardest materials, including molybdenum and tungsten. Wire EDM products are not affected by the hardness of the material, and can process conductive materials that cannot be processed by other processes, and the material can be heat-treated and then processed, avoiding the deformation problems caused by the post-heat treatment of the product.
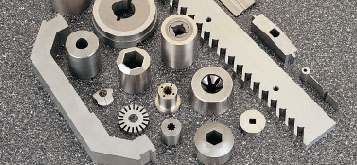
4. Low Requirements On Product Shape
In addition to the influence of metal wires and gaps at the inner corners of the product, wire EDM can easily cut precise and complex shapes even in the hardest or most fragile materials, while maintaining a low Ra Surface roughness.
5. Obtain High Tolerances
Wire cutting processing is more precise than laser, flame cutting or plasma processing. It does not exert any force on the parts, so that wire EDM can achieve very high tolerances to achieve precise dimensions and precise fit. This eliminates the need for additional machining and finishing of parts after machining.
6. Save Cost
Since wire-cut electrical discharge machining can be used to efficiently process any conductive material, the processing will take less time. In addition, wire EDM can also reduce waste. Since the metal wire is only about 0.3mm, the knife edge of the product after processing is very small, which greatly improves the material utilization rate and reduces the material cost. In addition, less waste is generated and no heat treatment is required, so cleanup can be minimized.
7. High security
The working fluid of wire cutting is non-flammable liquid, which can realize unmanned operation. Built-in induction and intelligent automatic control enhance the ease of use.
Disadvantages Of Wire EDM
Wire EDM, like other processing methods, has many advantages and some minor disadvantages.
Due to the nature of the method to achieve cutting, that is, the use of rapidly repeated controlled charges to corrode material along the cutting line on the workpiece along a bundle of wires to remove material, so EDM is limited to cutting conductive materials. Therefore, any composite material or material coated with a dielectric is not feasible for wire EDM.
The electrical conductivity that must be maintained when cutting parts with wire-cut electric discharge tools requires that the parts be firmly fixed in place and cannot be moved. In addition to the significant risk of deforming the pipe, this can also cause the cutting line to contact the workpiece, which can short-circuit the cut and break the cutting line, and cause “steps” in the workpiece. Although you can fix a test tube so that it can be rotated in an EDM machine, this method is optimized for more complex shapes and is not cost-effective for simple 2-axis pipe cutting.
Should you use Wire EDM in production?
Before choosing the right processing method for your project, there are some questions to ask. Wire-cutting machine tools represent a considerable investment and require well-trained personnel for programming and operation. These considerations should be weighed against the lower cost or less precise metal cutting methods of using CNC production services.
Some reasons for choosing wire EDM technology include:
- Create single high-quality parts for inventions, prototypes and proof-of-concept models
- Need to use a variety of hard materials and alloys with different thicknesses
- Requires extremely high-quality surface treatment and reduces post-processing of parts
- Copy or restore rare or unavailable parts used in cars or historical replicas
- Producing complex and highly detailed precision parts, which can be accurately repeated and copied in the next production run
- When the precise assembly and appearance of parts are critical to the final product, avoid part differences between different production batches and manufacturers
- Reduce cutting waste in expensive materials (such as gold, silver or expensive alloy materials)
- Produce thin, tapered holes, extremely narrow grooves or 3-dimensional shapes to perfectly fit existing parts
- Use computer-controlled processing to automate complex cutting and part manufacturing processes
- Meet extremely strict tolerances and material restrictions in aerospace or medical applications
- Use very small fragments or fragile materials that cannot withstand cutting pressure or stress
Related Post: What’s the Difference Between WEDM-LS, WEDM-MS and WEDM-HS?
What Is EDM Machining? Wire EDM 101