Tool deflection is one of the common challenges in CNC machining. It will cause machine chatter, destroy the surface finish of processed parts, and destroy dimensional accuracy. Generally, the tool is firmly placed in the chuck, but during operation, the reaction force of the material often exceeds the operating force of the tool, which may push or deflect the tool in an unexpected direction.
In order to produce parts with precision, precision and high-quality surface finish, it is important to minimize tool deformation. When the cutting force exceeds the rigidity of the tool, tool deflection occurs, causing the tool to bend. During operation, the tool may not feel bending, but it must be proven in the final test. Parts made with deflection tools may deform, exceed tolerances, be susceptible to changes, or exhibit a “cracked” surface finish.
Therefore, if tool deflection occurs, it may cause some errors in the CNC machining process. This is why it is necessary to fully understand what tool skew is, what its causes are, and strategies to reduce it. This article discusses all these factors to minimize tool skew.
What is tool deflection?
The tool deformation is just the name. This is the deviation of the tool from its intended alignment. The CNC machining cutting tool is tightly fixed in the chuck. This means that one end of the tool remains inside the chuck, while the other operating end of the tool is free or cantilevered. Because in CNC machining operations, the tool always exerts force on the workpiece, so the workpiece material also provides resistance. CNC tools are affected by different operating forces along with resistance. Therefore, if the rigidity of the tool cannot withstand the external force, the tool will deviate from its set alignment.
Tool deflection will definitely cause the following errors in CNC machining.
Catastrophic failure of tools or artifacts
Tool life cycle exhaustion
Size error
Rough surface or potential surface damage
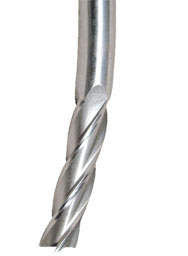
Strategies to prevent or reduce tool deflection
Although tool skew cannot be avoided 100%, it can still be reduced by using some strategies and strategies. CNC machinists can use the following proven strategies to reduce tool deflection during work.
Minimize the extension length:
The distance between the clutch point of the CNC tool and the operating tip of the tool is called the extension length. Since the tool is installed as a cantilever beam, it is always subject to bending stress and external vertical and horizontal forces. According to the stress theory of cantilever beams, the shorter the overhang length, the smaller the influence of bending stress. Based on the concept itself, the minimization of tool overhang length helps reduce tool deflection. These factors should be balanced with the details of the part geometry and processing requirements.
Enhance the core strength of the tool:
The core strength of the tool depends on its flute length and range. The difference between groove length and extension defines the stiffness of the core. Therefore, for CNC machining operations with uniform radial, long groove tools have good performance. If the core diameter is kept thicker, more material walls will be provided to absorb the shear stress, so the core strength and rigidity will eventually increase.
Enhance tool stiffness:
In the tool stiffness category, there are multiple effects, including tool condition, tool material, and tool size and shape-number of blades, core diameter and tool holder diameter. If the tool is worn and blunt, the cutting efficiency will be reduced, and more force will be required to achieve the same cutting and finish as a sharp tool. Therefore, more tool deflection occurs. High-quality tools made of stronger materials can reduce tool deflection. Finally, tools with larger diameters, and more specifically larger core diameters, are harder. Therefore, the largest tool allowed by the part geometry should be used.
It is not always possible to use larger or shorter tools. Certain operations may require tools with long distances or long grooves. In these cases, the tool should match the operation. For deep machining that requires the smallest cutting surface, long-distance tools with larger diameters and harder handles are more suitable. On the other hand, the operation of seamless walls requires long-slot tools.
In summary, optimizing tool selection and setting geometry to minimize unsupported length and maximize tool stiffness can reduce tool deflection, thereby improving part quality and reducing tool costs.
These are strategies to reduce tool deflection during CNC machining. However, high-quality CNC machines, high-quality tools and experienced operators can ultimately help reduce tool deflection.