In the mechanical manufacturing process, precision machining includes fine grinding, polishing, super finishing, grinding, honing and fine boring and reaming. Cooling lubricant is used in the middle of these machining. It is very important to pay attention to maintaining the inherent characteristics of the coolant in use, which depends on filtration.
Determination Of Filtration Accuracy
The filtering accuracy of the coolant is generally measured by the particle size or amount of the residual debris in the filtered liquid. The measurement method is to transfer the debris deposited on the bottom of the liquid tank to the filter paper (or use Filter paper to filter a certain amount of clean liquid); after drying, observe the size of the debris particle size with a microscope. The average value of the 5 largest particle sizes can be taken, and it is best to enlarge them and take photos for storage. There are also commonly used simple methods, such as PPM (parts per million) and MPL (mg/L) method, that is, the ratio of the weight of the solid particles remaining in the clean liquid to the weight of the liquid or the volume ratio between the two.
The measurement method of MPL is to take 1 liter of the filtered liquid and filter it with filter paper, leave the crumbs on the paper, and weigh the weight (mg) after drying. If the weight of crumbs is 50mg, then MPL is 50, and the percentage can also be used. Said.
The PPM measurement method is to put the filtered clean liquid into a long straight glass tube, let it settle for precipitation, and then measure the height of the deposition of debris and the height of the liquid surface to find the ratio of the two. If the height of the slag is 0.5cm, and the liquid level is 50cm, then 0.5/50-1 (by volume). That is, the slag content in the liquid is 1000PPM.
Commonly Used Filtering Methods
1. Features of precision machining coolant
(1) The cutting chips of grinding, honing, polishing and super-finishing are extremely fine particles, usually suspended in the coolant. If the workpiece is made of cast iron material, the chips are combined with graphite to make the coolant appear black liquid, and it can be filtered clean and clarified by general filtering treatment.
(2) Coolant crumbs in casting processing are fine and uniform, and contain graphite. If organic oil is mixed into it, it is easy to produce floating matter or form graphite iron powder slurry, which can easily block the filter.
(3) Ferrous metal processing coolant. The crumbs are finer, or they may be large strips.
(4) For non-ferrous metal processing, crumbs are generally large strips, and are also mixed with finer powder.
2. Commonly used filtering methods
Selection of filters, it is usually determined according to the size of the debris particles required in the cooling lubricant and the amount of filtration and purification required per unit time. The following describes the characteristics of several commonly used filtering methods.
(1) Precipitation method
A sedimentation tank or sedimentation tank can be used, which requires a larger area and a longer sedimentation time, so the container is generally rectangular with several sedimentation tanks in the middle. The container should not be too deep, otherwise crumbs are allowed to sink to the bottom of the pool. The coolant return pipe should be placed at one end of the container and extend to the middle of the liquid surface, and the pump should be placed in the clean liquid tank at the other end. Precipitation filtration is the simplest and coarsest filtration method, suitable for most rough processing.
(2) Magnetic separation method
Use a few high-energy circular permanent magnets or magnetic rollers to aim at the narrow area of the coolant return and keep rotating to capture the ferromagnetic particles in the fluid. It can also take away some non-magnetic particles, such as sand particles, to form a slag slurry from the scraper. Flow out of the board. The separable particle size is 80-100/micron, which is suitable for filtering coolant containing ferromagnetic slag during machining.
(3) Vortex separation method
It is a filter with a vortex forming surface and a cone-shaped guide head. The used coolant is pumped in the tangential direction of the filter head by pump pressure. The centrifugal force generated by the pressure generates the vortex to separate the dirt particles from the liquid, and Make crumbs sink along the wall of the conical tube to the bottom, clean liquid overflows from the middle of the tube to the clean liquid tank, about 1 to 3% of the liquid flows out along the small holes of the tube bottom with crumbs, so the filter device should be reasonable The arrangement can receive better results. In this way, a part of the liquid can be recovered after the filtered slag liquid is precipitated, and at the same time, the dirty liquid and the clean liquid tank are separated without mixing the two.
This filter has a filtration accuracy of 20-40 microns, which is suitable for general finishing, but it is not suitable for filtering long strips or lighter specific gravity such as graphite in cast iron, aluminum chips and fluffy produced in grinding processing. Chips and slag affect the filtering effect and block the slag discharge holes.
(4) Centrifugal separation method
The working coolant flows back into the high-speed rotating drum. The centrifugal force forces the heavy particles in the liquid to attach to the outer wall of the drum. The clean liquid overflows from the top of Jianxin. The filtration accuracy is 10-20 microns. The problem is that Shifts clean up the slag on the wall of the drum, but there are also automatic slag discharging machines abroad. The capacity of the system is small, and the filtering capacity is 2O~90L/min, which is suitable for small flow filtering of precision machining coolant.
(5) Chain plate conveying sedimentation tank
The cooling liquid flows back to the sedimentation tank after working. The tank is divided into several sedimentation tanks with some partitions, but the bottoms of the sedimentation tanks are connected. The chain drives the chain plate through the bottom of the groove and scrapes off the sediment on the bottom surface to the chip box, which better solves the problem of cleaning the sediment box, and is suitable for general grinding or machining.
The Development Of Filtration Technology
Due to the continuous progress of processing technology, people’s understanding of the filtering effect of precision machining coolant is also deepening. The filtering of cutting coolant not only needs to remove the debris, but also make the remaining debris in the fluid meet the predetermined process requirements. Moreover, it should be able to remove oil slicks or floating objects on the liquid surface, dissipate the heat drawn by the coolant from the processing area, and keep the coolant clean, clear and room temperature. Therefore, the filtering technology of the coolant has also been developed. For example, paper belt filters are widely used abroad.
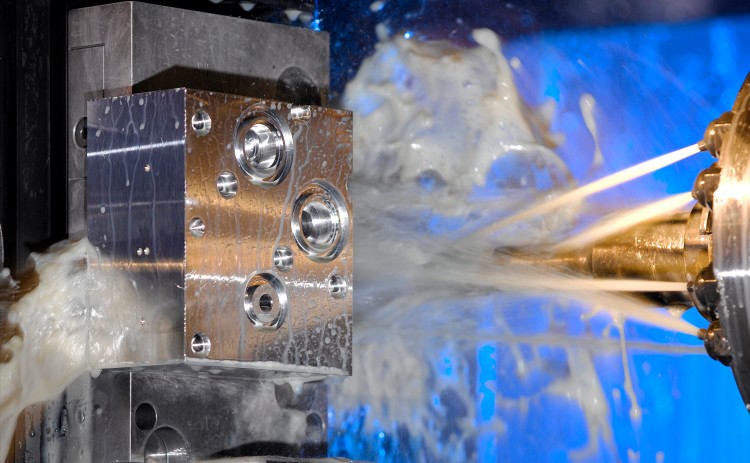
1. Gravity paper belt filter
It is characterized by the use of paper as a filter medium. The paper is made of inorganic fibers, also called non-woven or non-woven fabric, and uses its pores to filter the coolant. It is characterized by wide applicability and is not limited by filtering materials. Filter papers of different densities can be selected according to the requirements of different filtering precisions, which can easily achieve higher filtering precision.
This kind of filter has better heat dissipation, chip removal and oil absorption effects on the coolant, and is suitable for various precision machining of medium and small flow coolant filtration. Its flow specifications are 25, 50, 75, 100, 150, 200L/min, and its filtration accuracy depends on the density of the filter paper. When selecting filter paper, in addition to selecting the specifications of the non-woven fabric according to the width of the filter, the density of the non-woven fabric (g/m.) should also be selected according to the filtration accuracy required by the process.
2. Negative pressure paper belt filter
The working principle of negative pressure paper belt filtration is to inject the coolant to be filtered into the filter box through the dirty liquid inlet. The bottom of the filter box is covered with a filter medium and non-woven filter paper. It is supported by a stainless steel grid, and a conveyor scraper driven by a chain rests on the filter paper, which can move together with the filter paper.
This filter does not need a vacuum pump to form negative pressure naturally. Compared with the gravity filter, the filtering capacity and filtering accuracy are improved. It is a more advanced filtering method today.
3. Multi-stage filtration system
In order to improve the filtration efficiency and filtration precision of the coolant, it is often difficult to achieve both goals in one filtration. Coarse filter and fine filter are often used in combination in coolant filtering system. That is, first use a coarse filter to remove a large amount of slag in the coolant, and then use a fine filter to achieve the required filtration accuracy, and even use some auxiliary facilities to remove floating objects or slick oil in the coolant. The multi-stage filtration system uses two or three filters in series to perform coarse and fine filtration, for example, vortex separation, paper belt filtration, chain chain plate, sedimentation tank, paper belt filtration, or magnetic separation, paper belt filtration, and sedimentation box This type of filter device has been widely used in current precision processing equipment.