Numerical control processing technology originates from conventional processing technology and is an organic combination of conventional processing technology, computer numerical control technology, computer-aided design and auxiliary manufacturing technology. Due to the continuous development of technology, more and more parts need to be precisely processed in modern manufacturing, and the requirements for processing accuracy and surface complexity of the workpiece are also getting higher and higher. Therefore, CNC machining has received widespread attention, but in terms of cost savings, CNC machining is still more expensive than traditional machining. Now we will introduce the differences and advantages of CNC machining VS traditional machining.
The Difference Of CNC and Conventional Machining
1. Operation method
The CNC system consists of software and hardware. The operator uses the software to monitor the machine tool and create programs. The NC program is a list of instructions that instructs the machine how to handle the parts. The NC hardware reads the program and tells the machine how to operate.
Traditional machining means that the operator directly controls all movements of the machine tool. The operator can choose when to move the equipment. He also decided to stop the feed, when and where to stop. Operators use special rulers and gauges embedded in the control rod to improve accuracy.
2. Cost and output
The conventional machining cost is low, and it is usually used for small batch projects. CNC machining is used for mass production and is not cost-effective for smaller projects.
3. Replication
CNC – After correct programming, the CNC machine can produce the same final result as many times as needed. The high production quota greatly benefits from CNC functions.
Due to human factors, traditional machining (very suitable for making a single customized part), it is impossible to make an accurate copy using traditional machining.

4. Labor Required
CNC Machining- With proper training, CNC operators can supervise multiple machines at once. After the machines are programmed, they can do the work on their own-almost without human intervention.
Conventional Machining – Mastering conventional processing technology requires a wealth of knowledge, training and talent-with different skills (usually multiple people) required to complete different parts of the process. In manual lathes, each machine must have a skilled technician.
5. Accuracy
CNC Processing- Since production is software-based, CNC machines can manufacture parts that are almost impossible to produce by hand or traditional machining methods. Eliminating the factor of human error means that it can be cut precisely every time, greatly reducing the chance of error, reducing product waste, and ensuring quality!
Conventional Processing-The final result of conventional processing depends entirely on the skill level and experience of the technicians.
6. Processing Technology
In ordinary machining process, whether it is positioning datum, clamping method, tool, cutting method, etc. can be simplified, but the data processing process is more complicated, and these factors need to be fully considered. The same processing for tasks, the CNC machining process can have multiple schemes, which can arrange multiple machining parts and machining tools as the main line. The process has diversified characteristics. This is the difference between the CNC machining process and the traditional machining process.
7. Clamping and fixture
In the CNC machining process, not only the coordinate directions of the fixture and the machine tool must be relatively fixed, but also the dimensional relationship between the parts and the machine tool coordinate system must be coordinated. Moreover, the two steps of positioning and clamping need to be effectively controlled during the clamping process. Under the traditional machining process, due to the limited machining capacity of the machine tool itself, it is necessary to perform multiple clamping during the machining process.
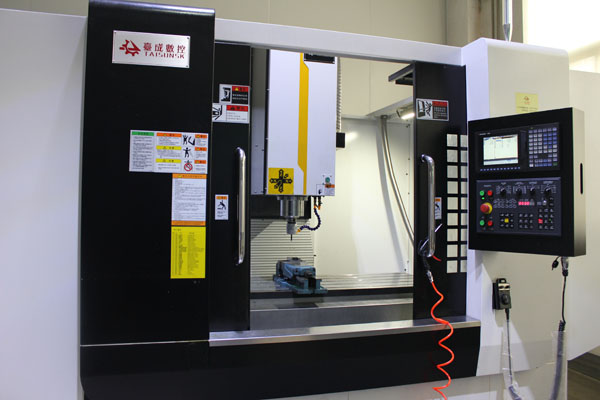
In addition, it is necessary to use special fixtures, which leads to higher costs in the design and manufacture of fixtures, and virtually increases the production cost of products. The positioning of the CNC machining process can be debugged by the instrument. In most cases, no special fixture design is required, so the cost is relatively low.
8. Cutting Tool
In the process of machining, the choice of cutter tool needs to be determined according to the processing technology and processing method. Especially in CNC machining, the use of high-speed cutting is not only conducive to the improvement of machining efficiency, but also the machining quality can be guaranteed, effectively reducing the probability of cutting deformation and shortening the machining cycle, so the demand for cutting tools under high-speed cutting further increases .
Advantages Of CNC Machining Over Conventional Machining
It is not surprising that many manufacturing companies have recently shifted their traditional processing to CNC processing. Because automotive intelligence, medical care, military and aerospace industries all require precision parts, their tolerances must be strict to +/- .0005, which is difficult to achieve with traditional machining. Next, let’s take a look at the advantages of CNC machining compared with traditional machining.
1. Worker safety
The CNC machine operator can protect any sharp parts behind the protective structure. The operator can see what is happening on the machine through the glass. The operator does not necessarily need to be close to the spindle or milling machine. The operator does not have to be close to the coolant. Depending on the material, certain liquids are dangerous to human skin.
2. Reduce labor costs
In the case of conventional processing, each machine requires specialized technical personnel, who should have experience, skills and extensive knowledge of the opponent’s machine. In contrast, CNC machining is strictly controlled by the software program, and almost no manual intervention is required except for the initial setup and data feed.
The operator only needs to check for errors in the settings or programs. This situation means that there is free time between operators, which can be used to operate more tools. One operator can use several machine tools, you can save the cost of hiring more people to operate the machine tools, while still maintaining a high level of production.
Because computers play an important role, the chances of human error and workplace safety compromise are greatly reduced.

3. Excellent reproducibility
CNC machine tools are designed to control precise speed and positioning, and can produce thousands of 100% identical parts in record time, a feat that cannot be achieved with handheld or traditional machining. The machine can be programmed to repeat the same cut or repeat the same finishing without affecting the quality of the processed part.
When you need to make a single custom part, conventional machining works well, and conventional machinery requires the help of experienced operators to make similar parts. Even so, there are still small differences between the parts.
4. Large quantity and good quality
Due to the need for labor, traditional machining is mainly used for small batch and small batch projects. However, whether it is producing dozens of metal processing parts or thousands of metal processing parts, CNC machine tools can provide the highest accuracy.
Numerically controlled high-quality materials make them resistant to wear and tear, which is common in conventional machining. As a result, they can operate 24 hours a day and are maintained promptly but quickly. In addition, CNC machining uses advanced software, which can be updated regularly according to specifications to make the manufacture of ultra-complex parts easier.
The CNC machine also has an automatic cooling system to reduce the chance of thermal damage. Many advanced machine models have built-in chip storage and conveyor belts for chip management.
5. No prototype required
A prototype is needed to simulate the design and draw its feasibility diagram. Before CNC machining, each manufacturer will develop a feasible prototype, conduct a trial run, and then proceed to the machining process. If done manually, the entire routine usually takes days or even months. The introduction of CNC machines introduces software programming, where you can enter a design and intuitively see if you can use it in actual situations. This means there is no need to pay any additional costs for prototype development, saving weeks or months of production time.
6. Ability to develop complex parts
CNC machines can be reprogrammed and updated at any time, so that they can freely and easily produce 3D, 4D and even 5D parts. If required, this can make a smoother transition between the production of conventional CNC machined parts and the production of complex parts. In addition, the software can store designs, so you can revisit any desired shapes or other designs more quickly.
7. Higher cutting parameters
Now, high-speed cnc turning can be performed through the enclosed cutting area. The chips fly at high speed and then spray coolant at high pressure during processing. When the speed reaches 10000 rpm or higher, manual operation cannot be performed. Since the cutting speed is very fast, the chip width and feed rate must be kept stable to avoid vibration, which cannot be done manually.
8. Many choices of materials
This may be the biggest advantage of CNC machining over traditional machining. CNC machines can use almost all types of materials, including metal, steel, wood, foam or sensitive plastic.
9. High processing accuracy
CNC machining can provide top precision, precision and speed for high and low volume products, which is a very advantageous choice for manufacturers in various industries. The traditional manual milling machine has a machining accuracy of +/-0.05mm, while the CNC machining center can reach 0.005mm, 0.003mm or higher precision. (Related Post: What is CNC Machining?)
SANS has both conventional and CNC machining, as a machining factory for more than 10 years, we specialize in Custom Machining Manufacturing, we will based on your files to choose the most suitable process which can save your time and cost. Contact For Free Quotation Now.