Although copper, brass, and bronze are completely different alloys, they may appear the same at first because they have many common features, so they are often collectively referred to as red metals.
Copper
The minimum copper content of the copper alloy is 99.3%. They are good thermal and electrical conductors and are commonly used in busbars and wire connectors in electrical applications.
Copper is used in many products because of its excellent electrical and thermal conductivity, good strength, good formability and corrosion resistance. Due to their corrosion resistance, pipes and fittings are usually made from these metals. It can be welded and brazed, and can be polished and polished to give it almost any desired texture and gloss.
Copper also has good resistance to bacteria. After extensive antibacterial testing by the Environmental Protection Agency, it was found that within two hours of contact, 355 copper alloys (including many brass) were found to kill more than 99.9% of bacteria. It was found that normal tarnishing does not compromise the antibacterial effect.
Brass
Brass is mainly an alloy composed of copper and zinc. Brass can be added with different amounts of zinc or other elements. The mixture of these changes will produce a wide range of characteristics and color changes. The increase in zinc content provides the material with higher strength and ductility. High zinc content can improve strength and ductility, while the addition of manganese can improve corrosion resistance. Lead is a common additive in brass that can improve its machinability and other unique elements that make up the brass alloy category.
The color of brass ranges from red to yellow, depending on the amount of zinc added to the alloy.
If the zinc content of brass is between 32% and 39%, its hot workability will increase, but cold work will be limited.
If the zinc content in brass exceeds 39% (for example, Munz metal), it will have higher strength and lower ductility (at room temperature).
Common types of brass available include: red brass, yellow brass, 330 brass, 360 brass, 464 brass, etc.
Brass Characteristics
Compared with bronze, brass has higher ductility, making it ideal for applications requiring high formability. On the other hand, it also shows a significantly lower melting point (900 degrees Celsius).
Depending on the alloy, its density is about 8.73 g/cm3, and its melting point is as low as 900-1000°C. Brass is an important conductor of heat, and it is resistant to corrosion, especially to the corrosion of seawater in the galvanic battery. It has good casting properties, is quite durable and attractive, and because of its high copper content, it even has certain antibacterial properties.
The bright, golden appearance of brass makes it an excellent choice for decorative applications. Its workability and durability make it very suitable as a raw material for musical instruments. The high corrosion resistance exhibited by brass makes it suitable for plumbing applications. Similar to bronze, brass is used in electronic applications because of its excellent electrical conductivity. (Related Post: All About Brass Machining CNC Machined Parts)
Bronze
Bronze is an alloy composed mainly of copper and other components. In most cases, it mainly contains copper and 12% tin, but arsenic, phosphorus, aluminum, manganese and organic silicon can also be used to create different properties in the material. The alloy produced by these components is much harder than copper alone.
The typical bronze color is reddish brown/dark gold and is brittle, but not as good as cast iron. Its relative density is about 8.8 g/cm3, and it has low friction when in contact with other metals. It conducts heat and current easily, and has a melting point in the range of 950-1050°C, depending on the tin content. Due to its high copper content, it will oxidize in the air, giving the bronze a distinctly mottled patina. This oxidation prevents bronze corrosion, especially in salt water environments.
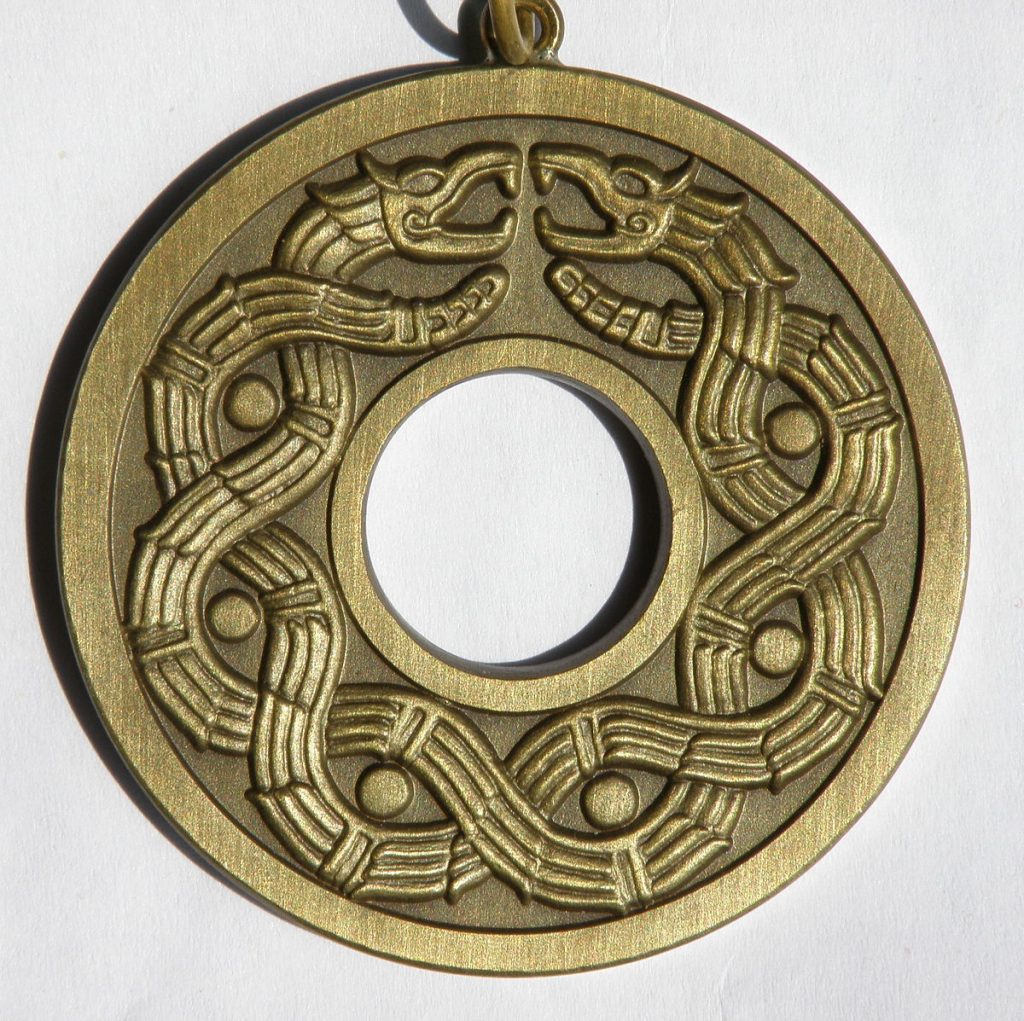
The high corrosion resistance to salt water allows bronze to be used for marine accessories and underwater parts, as well as sculptures that must resist degradation in the external environment. It has excellent casting properties and can be easily cast into bearings, clamps, electrical connectors, springs, etc.
The dull golden hue of bronze makes it a popular material for sculptures and other artistic creations such as bells and films.
Some bronze alloys are particularly suitable for electrical applications due to their excellent electrical conductivity.
The low metal-to-metal friction of this material makes it suitable for high stress environments such as those experienced by bushings and bearings.
Difference Between Brass and Bronze
The differences in material compositions between bronze and brass result in varying characteristics that make them suitable for different use cases.
Below is a Comparison Chart that will clearly highlight the similarities and differences between the two metals: (source from henssgenhardware.com/brass-vs-bronze)
Brass | Bronze | |
Composition | Brass is an alloy of copper and zinc. | Bronze is a metal alloy consisting primarily of copper, usually with tin as the main additive, but sometimes with other elements such as phosphorus, manganese, aluminum, or silicon. |
Properties | Higher malleability than zinc or copper. Low melting point (900 c); flows when melted. Combinations of iron, aluminum, silicon & manganese make brass corrosion resistant. Susceptible to stress cracking when exposed to ammonia. Not as hard as steel. | Hard and brittle. Melts at 950 centigrade but depends on amount of tin present. Bronze resists corrosion (especially seawater corrosion) and metal fatigue more than steel and is also a better conductor of heat and electricity than most steels. |
Color | Muted yellow, somewhat similar to gold, but duller. | Reddish brown. |
Uses | Decorative; Low-friction applications (locks, gears, doorknobs, ammunition, valves); Plumbing / electronics; Musical instruments for acoustic properties; Zippers & uses where it’s important to negate spark (fittings & tools around explosive gas), boat and marine hardware | Used in boat and ship fittings, propellers and submerged bearings because of resistance to salt water corrosion. Widely used for cast bronze sculpture; Bearings, clips, electrical connectors and springs; For top-quality bells and cymbals. |
History | Brass was first known to exist in about 500 BC. | Bronze dates to about 3500 BC. |
With many years of experience and proven expertise, our brass machining capabilities enable us to deliver high precision parts and components that match your design specifications. We can provide CNC Milling, Turning, Grinding and EDM Service for Brass machining. If you needed, send us drawings for free quotation now.