In actual operation, CNC machine are mainly used to manufacture workpieces, and the workpieces usually have extremely high machining accuracy. If you want to improve the machining accuracy of the CNC machine itself, you must analyze the errors that may occur in each step of the CNC machining, and the purpose is to find the root cause of the error, so as to avoid the continuous generation of errors. You can also formulate corresponding measures according to the analyzed reasons, and compensate immediately once there is an error. In the entire CNC machining project, whether it is the initial drawing stage or the final product finalization, errors in any step will have a certain impact on the accuracy of the final machined parts.
The following will discuss several main errors that frequently occur, discuss the reasons for the errors and how to improve them.
1. Errors that are easy to appear in actual operation
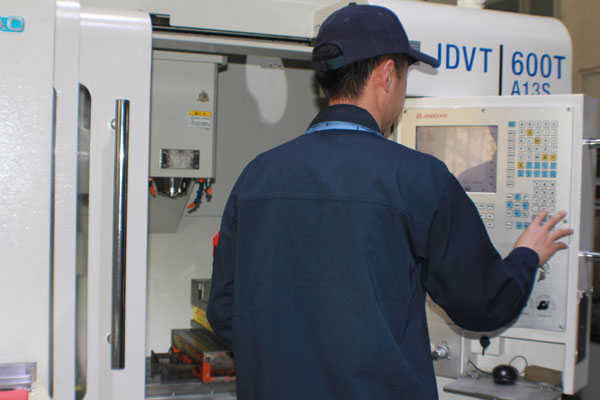
1.1 Programming Error.
This error is mainly caused by the process of CNC programming software, which is a kind of interpolation error. When using CNC machine to process parts, because the CNC devices have different interpolation functions, they are different from the contour of the part. When approaching each other, they always choose a straight line, and sometimes they use a circular arc.
When a straight line or arc is approaching the contour curve of a part immediately, there will be a maximum difference between the approximation curve and the original curve of the actual contour. This is commonly referred to as interpolation error, which affects the machining accuracy of the part. Among the factors that affect the machining accuracy of the parts , this is a very important reason.
1.2 Tool nose Arc Error.
In the process of cutting the inner hole, when the operation goes to the outer circle, the tool tip arc usually does not affect the size and shape. However, when process the tapered surface or arc, the arc of the tool tip will affect it, which generally leads to overcutting or undercutting.
1.3 Measurement Error.
This error is usually affected by the measurement accuracy of the measuring tool, and it may also have a certain impact because the measurer has not adopted the correct operation method for the measurement. The actual measured size usually has a deviation.
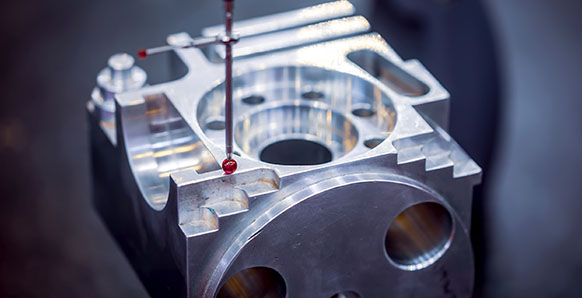
1.4 Tool Wear Error.
When the CNC machine is working continuously, the parts and materials to be processed and the tool itself are in a high temperature and high pressure environment, and will generally wear out the tip of the tool, which will also cause certain errors. At the beginning of work, the speed of tool tip wear will be faster, and then it will become smaller and smaller, until finally there is a trend of gradual acceleration again.
1.5 Error Caused By Reverse Loss Of Momentum.
CNC machine cause errors due to the gaps between the machines and the elastic deformations between the transmission parts of the machine tools.
1.6 Tool Setting Error.
The main process of this kind of error is in the tool setting process. When the tool starts to move to the starting point, the operating system will generate a certain feed adjustment ratio value. This value will affect the deviation.
1.7 Machine System Error.
The machine body can have a certain influence, which leads to the appearance of geometric tolerances, which are usually impossible to adjust. In the servo unit, the drive device will have a certain repetitive positioning error during work. The reason is that the pulse equivalent of the machine tool has a certain impact on the system. The uniformity and transmission route will affect the system, but the above two The amount of error is relatively small and stable, and it only needs to be considered during precision machining.
2. Improve Operation Method
In the actual operation, it is impossible to avoid any errors in machining parts of CNC machine tools. However, if certain improvements are made in the operation of CNC machine tools, then certain errors will be effectively controlled within a reasonable range.

Program Process
Before the parts are processed by numerical control, it is necessary to write a processing program with a certain degree of feasibility. Generally speaking, there are two ways to write a program. One is manual programming and the other is computer-aided programming.
Manual programming is usually only suitable for the preparation of simple part programs, and there is generally no deviation in this link. Computer-aided programming is for the writing of demanding and complex part programs, but due to the need to use the corresponding software to set the tool change point and trajectory, there will inevitably be some problems, which requires extremely high modification settings. At the same time, pay attention to whether the program has extremely high feasibility. These aspects may cause errors. Generally speaking, increasing the number of nodes can effectively solve such problems, but it will also increase the workload of programming. Greatly increase, and the processing efficiency will be greatly reduced.
The level of program efficiency has a large impact on the working efficiency of the machine. Therefore, optimizing the programming quality can also improve the working efficiency of the CNC machine. This requires familiarity with all the instructions of the machine and the Internal functions are thoroughly developed, and effective programming methods are constantly being explored. In addition, computer programming must be promoted vigorously, and the reliability of the program must be continuously improved. Another point is that the programming must be reasonable, and do not allow the machine tool to run empty.
Tool Nose Radius Value
When the program is finished writing, it is necessary to pay attention to the problem of the tool nose radius value. Not only need to use the corresponding commands in the program, but also need to measure the tool nose radius value owned by the CNC machine. After the measurement, set it in the parameter setting page. Only after this process, the corresponding command in the CNC program The command can be used, otherwise, the default value of the tool nose radius in the system is always zero.
Cutting Tool Setting
The work that needs to be carried out afterwards is the knife setting, usually at the same time by trial cutting and knife setting. Choosing a tool can improve the processing quality on the one hand, and can also promote the improvement of processing efficiency. To increase productivity, CNC machine at home and abroad are developing towards high speed. This also puts forward higher requirements for the machine: it must be able to withstand high-speed cutting, at the same time it must have the function of powerful cutting, and the function must have extremely high stability. When selecting tool materials, if cemented carbide tools can be used for machining, then high-speed steel tools should not be selected. If conditions permit, tools with higher wear resistance can be selected.
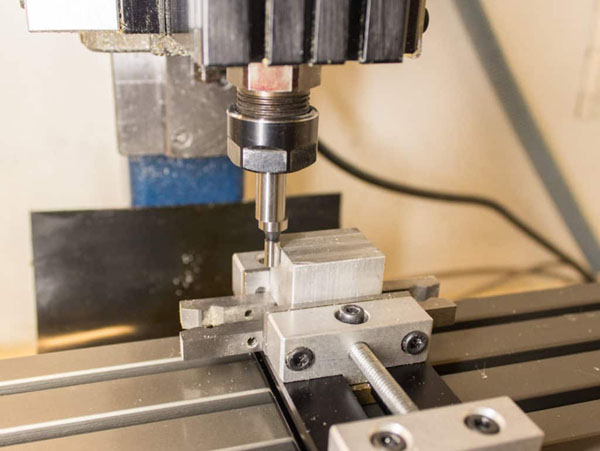
At the same time, the measurement must be carried out in a static environment, but the machining process is precisely dynamic. The tool and the workpiece are inevitably affected by external forces, so that the machined size and the expected size will be inconsistent. Therefore, we must pay attention to the material of the tool used, and always check whether the workpiece and the tool holder are clamped, and whether the length of the workpiece protruding from the fixture meets the standard.
CNC machine are very different from ordinary machine. It is not feasible to directly apply the methods used in managing ordinary machine to CNC machine. According to the experience of factories with a long service life, it is best to adopt centralized management for factories with a large number of CNC machine and arrange them according to production. If conditions permit, the computer can be used for integrated management, and the computer can perform unified management of all operating information, so that information can be shared, the preparation time required for production can be greatly reduced, and the productivity will naturally increase.
3. Conclusion
In the entire machining process, errors are unavoidable. However, if the operation method of CNC machine is improved, in the actual production process, whether it is the production and processing of small batches of parts, there are still medium precision requirements. All the parts can achieve the purpose of reducing errors, and the parts can also meet the standards required by the drawings. Whether it is the manufacturer of CNC machine, or the users and maintainers of CNC machine tools, they must pay sufficient attention to the machining accuracy of CNC machine. CNC machine usually have extremely complex error sources. This article only analyzes the most important ones and proposes more feasible measures to improve them.
Through the above experience summarization and analysis, hope can significantly improve the daily manufacturing, use and maintenance level of CNC machine. We believe that as more and better technologies are applied to the field of CNC machine, the existing error problems of CNC machine will definitely be solved more satisfactorily.