Under certain conditions, even the strongest metal parts may suffer corrosion, which occurs when the metal reacts with the surrounding environment. Any metal can suffer some degree of corrosion, although some metals will react in a different environment from others.
No metal is completely safe from the threat of corrosion. But importantly, corrosion can usually be prevented or minimized by following certain steps. These steps involve good product design, material selection and application of surface treatment.
This article discusses several methods to reduce corrosion of metal parts manufactured by CNC machining technology.
What Is Corrosion?
Corrosion occurs when metals react with oxidants in their environment. This chemical reaction causes the metal to degrade over time, thereby impairing its appearance and compromising its structural integrity.
Corrosion is the deterioration of materials caused by environmental interactions. This is a natural phenomenon and requires three conditions: moisture, metal surface and an oxidant called electron acceptor. The corrosion process transforms the reactive metal surface into a more stable form, namely its oxide, hydroxide or sulfide.
Each metal has different electrochemical properties. These characteristics determine the type of parts that are susceptible to corrosion. For example, iron tools that have been exposed to a humid environment for a long time are prone to rust, while copper roofs can rust under the influence of weather. Although some metals are more resistant to corrosion than others (depending on the environment), every metal is not immune to all corrosion effects.
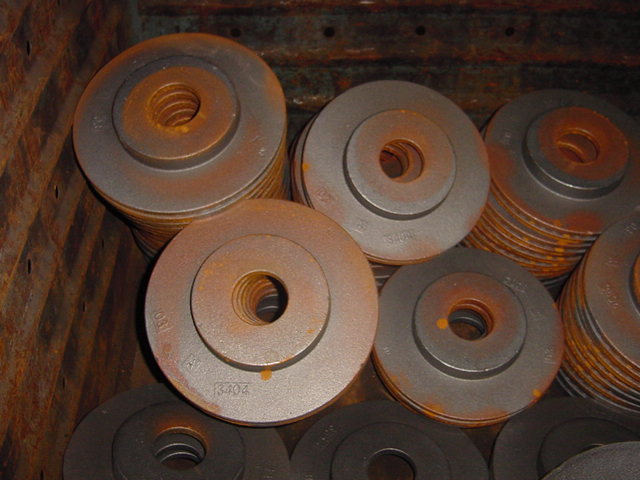
Bad Effects Of Corrosion
Corrosion can have various negative effects on metals. When metal structures are corroded, they become unsafe, which may cause accidents, such as collapse. Even minor corrosion requires repair and maintenance. In fact, the global annual direct cost of metal corrosion is approximately US$2.2 trillion!
Although all metals will corrode, it is estimated that the use of appropriate protection methods can prevent 25-30% of corrosion.
Corrosion is a natural process in which environmental conditions transform the refined metal into its oxide, hydroxide or sulfide form.
How To Prevent Corrosion Of Metal Parts
Steps can be taken to prevent corrosion of metal parts. Most of these steps are performed before and during the manufacturing process, but once they are used, corrosion of the parts can also be reduced.
Following these steps does not guarantee the unlimited life of the part, but it will reduce the potential for corrosion to some extent, while helping to maintain the normal function and appearance of the metal part.
You can prevent corrosion by choosing the right method:
- Metal type
- Protective coating
- Reasonable design
- Environmental control
- Sacrificial Coating
Metal Type
An easy way to prevent corrosion is to use corrosion-resistant metals, such as aluminum or stainless steel. Depending on the application, these metals can be used to reduce the need for additional corrosion protection.
Stainless steel: The iron in stainless steel will oxidize and rust. However, steel with high chromium content (for example, stainless steel 316) is not easy to rust because chromium forms a protective layer of chromium oxide on the surface of the part.
Aluminum: Aluminum does not contain iron, so it will not rust. A protective layer of aluminum oxide will be formed on the surface of the part when it encounters moisture to prevent corrosion.
Copper, bronze, and brass: Red metals such as copper, bronze, and brass contain little or no iron and will not rust. Oxidized copper exhibits a green patina. Although this may not be aesthetically ideal, it can protect copper components from corrosion.
Protective Coating
The coating can act as a physical barrier between the metal part and the oxidizing elements in the environment, thereby providing a layer of corrosion protection. Unless the coating itself is worn away, air, moisture and other corrosive substances cannot directly contact the metal. After a period of time, the paint can be reapplied to maintain the condition of the part.
A common method is galvanizing, where the manufacturer applies a thin layer of zinc on the part. For some metals, it may be best to add hard chrome plating (moderate price, good corrosion resistance) or black chrome plating (more expensive, with excellent corrosion resistance).
Paints and/or primers are a direct and inexpensive method of preventing corrosion, and may still be necessary for aesthetic reasons. The paint coating can act as a barrier layer to prevent the transfer of electrochemical charges from the corrosive solution to the underlying metal.
Another possibility is to apply powder paint. During this process, dry powder is applied to the clean metal surface. The metal is then heated to fuse the powder into a smooth, unbroken film. Many different powder compositions can be used, including acrylic, polyester, epoxy, nylon, and urethane.
Reasonable Design
Corrosion control starts at the engineering stage. If the part is to be used in an environment prone to corrosion, engineers should consider whether certain design features will encourage or prevent corrosion when creating a CAD design. The material of the part will affect its corrosion resistance, but the shape and texture will also affect the corrosion resistance
The designer should eliminate the narrow gap to prevent air or fluid from entering and stagnating. Avoid functions that may accumulate moisture or air. Parts should not contain deep cracks that can accumulate moisture, and if possible, encourage air flow. If parts absolutely must contain gaps, tunnels or other weak points, make sure that the metal can be maintained regularly.
Environmental Control
The post-manufacturing steps may be more difficult to implement than the pre-manufacturing steps, but once the part is used, it is still possible to reduce corrosion.
Corrosion is caused by a chemical reaction between the metal and the gas in the surrounding environment. By taking measures to control the environment, these adverse reactions can be minimized. It can control the content of oxygen or chlorine in the surrounding environment. For example, you can also prevent the parts from contacting excessive moisture by adjusting the position of the parts or introducing obstacles.
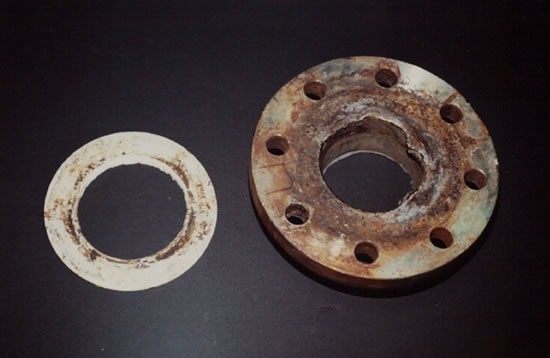
Sacrificial Coating
Another way to make parts resistant to corrosion is to apply a sacrificial coating to the metal instead of a protective coating.
The purpose of the sacrificial coating is not to completely prevent corrosion, but to make the coating corrode, not the underlying material of the part. Therefore, the coating is called a “sacrificial” material. There are two main technologies for achieving sacrificial coatings: cathodic protection and anodic protection.
Cathodic Protection
The most common example of cathodic protection is the coating of iron alloy steel with zinc, a process called galvanizing. Zinc is more active than steel and oxidizes when it starts to corrode, thereby inhibiting the corrosion of steel. This method is called cathodic protection because it works by making steel into the cathode of an electrochemical cell. Cathodic protection is used to transport water or fuel steel pipes, water heater tanks, ship hulls and offshore oil platforms.
Anode Protection
Anodic protection involves coating ferroalloy steel with a less active metal, such as tin. Tin does not corrode, so as long as there is a tin coating, steel can be protected. This method is called anode protection because it makes steel the anode of an electrochemical cell.
Anodic protection is often used in carbon steel tanks to store sulfuric acid and 50% caustic soda. In these environments, due to the extremely high current requirements, cathodic protection is not suitable.