Precision machining is a basic service that can be used to create parts and components of many tools that we use and rely on in our daily lives. All industries we serve require advanced processing, including aerospace, medical, automotive automation, etc. But what exactly is precision machining? Here, we introduce in detail what is precision machining, processing methods, advantages and why high precision machining is important.

What is High Precision Machining?
In the manufacturing industry, “high-precision machining” usually refers to parts whose tolerances are within a few micrometers. Precision machining process refers to various machining processes whose machining accuracy and surface finish are higher than those of the corresponding machining methods. Precision machining processes include precision cutting and high-brightness and high-precision grinding. The accuracy of precision machining is generally 10~0.1μm, the tolerance level is above IT5, and the surface roughness Ra is below 0.1μm.(What is CNC Machining?)
The real art of precision machining is the combination of computer control design and human engineering design, which can create unique functions and highly controlled output through the development of fluid dynamics, chemical control, machinery, extreme weather, and the durability required by modern hardware And functional technology. Precision machining is very important for manufacturing tools and parts in a precise and stable manner, and can be repeated, with consistency, accuracy and durability.
What is Precision Machining Used For?
Precision machining is a subtractive process used when material needs to be removed from the original product to make the final product. Precision machining can be used to create a wide variety of products, items, and parts for a variety of different objects and materials. These parts usually require strict tolerance changes between the nominal size and the parts, which means that there is not much room for error in the production of parts. It is used to compose many large and small objects and their components used in our daily lives. If the object is composed of many small parts, it usually needs to be precision machined to ensure that they fit together accurately and work properly.
Components, parts and finished products designed to maintain extremely tight tolerances and high durability are common driving forces essential to the use of precision machining. For example, parts that need to work together as machine parts may need to always be aligned within a certain range of 0.01mm to 0.005mm. Precision engineering and machining help to ensure that not only these parts can be manufactured accurately, but also that they can be produced with this precision time and time again.
Another common application of precision engineering might be when tools or components need to be repaired or repaired. After a period of use, the tools or components of the object may require machine calibration, grooving or welding to restore them to their original state. This can also be done by precision machining.
It can also be used in test fixtures, or automated production lines, especially in some high-precision industries, such as the electronics industry, automotive automation industry, medical machine production lines, etc. (Industries That Benefit From CNC Machining And Manufacturing)
What Tools And Material Are Used In Precision Machining?
Various raw materials can be used for precision machining, such as plastics, ceramics, metals, stainless steel, steel, bronze, titanium, tungsten, etc. For precise cutting and complex removal of raw materials, a variety of tools can be used. These tools depend on raw materials. For most materials, milling machines, lathes, grinders, other CNC machines, EDM, etc. can be used. All of these are mainly CNC controlled machines operated by highly qualified and experienced operators. Each tool has different functions, materials, size of parts, complexity of parts, surface treatment, etc. will affect the choice of tools used.
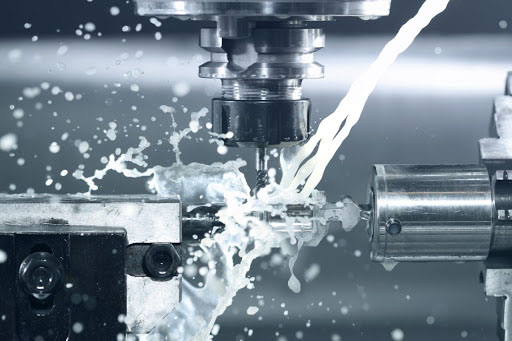
What Machines Are Used?
To get the best results from precision machining, it means the ability to accurately follow specific blueprints created using computer-aided design (CAD) or computer-aided manufacturing (CAM) procedures. CAD or CAM files are used to create the 3D drawings needed to produce parts. Due to the nature of precision machining, well-trained technicians must create files with very precise specifications. Then, this CAD or CAM file is used in CNC machining to obtain the best results in the machining process.
To manufacture these highly complex and high-precision parts, advanced machinery is needed to effectively do this. The various types of CNC machine capabilities include:
- 3-axis CNC machining
- CNC milling
- CNC turning
- Multi-axis CNC machining
- Indexed CNC machining 3+2 axis
- 5-axis CNC machining
- Precision Grinding
- EDM and Wire EDM
Precision Machining, the quality is also very important, so the inspection machine is necessary. Normal include:
- CMM
- Microscope
- Altimeter
- Micrometer
- Hardness Testing Machine
- Calipers
Advantage of Precision Machining
1. Operational Efficiency
The precision machining process largely depends on computer-controlled machines that can run automatically and at high speed without any manual intervention. This means that manufacturers can rely on less labor to process parts. Reducing production costs and improving product quality can improve the operational efficiency of the factory floor. However, operating advanced machines and systems requires skilled labor.
2. Increase Speed
Precision machining involves equipment that uses computer animation drawings to interpret blueprints and execute them accordingly. These machines can clearly outperform humans in terms of speed, accuracy and overall output. Most importantly, machines do not need sleep, because they can work for a long time.
3 Consistent Product Quality
Precision machining by CNC machine tools can ensure consistent output time. Consistently producing high-quality products can increase customer confidence and increase the visibility of your brand.
4. Reduce Risk Factors
Errors, whether human or mechanical, can slow down the entire production process and increase production costs. However, human error in the process can be eliminated by using smart machines. Since computers strictly follow a set of predefined operations, they are unlikely to go wrong.
5 Low Error
By using CNC machine tools, once the correct specifications are entered, the automated precision machining process will take over. Compared with manual processing, the chance of error is extremely low.
6 Low Production Cost
CNC machines are usually used to manufacture precision parts. The comprehensive nature of this manufacturing process reduces waste, reduces labor and reduces the possibility of errors. Due to low production costs, the manufacturing industry is now increasingly using automated systems to run its business.
7. Fast Production
We know how fast automated manufacturing systems can work and perform repeatable tasks with high precision. In terms of speed and accuracy, humans cannot beat precision engineering machinery. The shortened turnaround time helps the company meet market expectations and achieve sustainable growth.
Why High Precision Machining Is So Important?
With the rapid development of 5-axis CNC machining technology, more and more prototype manufacturers have put forward higher requirements for precision machining of parts. For example, if the size of the device is reduced, the components that make it work will continue to shrink to achieve better performance and higher efficiency. Many industries are eager to use micro-components in their products, which is a trend in industries including electronics, medical components, energy components and life science research. Any company that needs to cut durable parts into precise dimensions and ensure that they work in a larger system needs CNC machining to complete the work.

In recent years, the machinery manufacturing industry is developing towards precision machining and ultra-precision machining at a rapid pace of development. In the future development process, precision machining and ultra-precision machining will become the key technology to win in market competition. The main reason why modern manufacturing needs to improve processing accuracy is to improve product performance and quality, improve its quality stability and performance reliability, promote product miniaturization, strong functions, good parts exchange, product assembly, and debugging productivity High, and promote manufacturing and assembly automation. Industry automation and intelligent industrial upgrading and reform will undoubtedly increase the demand for precision parts.
Ready To Implement Precision Machining?
SANS machining, we offer contract CNC precision machining for many industries: automotive, optics & aerospace, military, transportation and more. As a factory with more than 10 years experience, we specialize in custom precision machining in milling, EDM, WEDM and Grinding process, also can provide Jig&Fixture and parts assembly service.
Send Your Drawings For Free Quotation!